We will work to consistently communicate with our customers and to provide environmentally friendly, high-quality products and services that are trusted by, and satisfy, our customers.
Quality Philosophy and Quality Policy
Quality Philosophy
Quality Policy
Quality Control
Under the quality philosophy “We will endeavor to develop and enhance technologies and to supply high quality products in response to the needs of customers,” the company conducts business activities based on the principles “customer first” and “quality first,” and its quality policy.
We uphold Jikotei Kanketsu (defect-free process completion) as our basic principle to ensure that no defects are passed along to the next process and that our customers are satisfied with our products. To establish a quality assurance system that meets global standards, quality is built into all processes starting with the preliminary design and production stage.
In August 2019, we opened the “Study Hall” to foster the next generation of manufacturing human resources and established the “Quality Dojo.” We are deepening our specific knowledge of quality and working to improve quality by learning from defective products of the past and educating customers about their factory processes (post-processes).
In addition, we continue to engage in the “START” project, the global quality improvement initiative to prevent future defects, and the Smart Standard Activity (SSA) to optimize quality standards by recognizing the gap between customer (end-user) needs and the value provided.
In 2021, SSA added “Closeness Activities,” in which Toyota Motor Corporation, our main customer, actively listens to the problems of our suppliers, and it has become a valuable pillar of our activities that has produced many positive results. Recently, we expanded our activities to overseas bases and are conducting a review of appropriate quality.
In addition, all our offices and plants in Japan have obtained certification for ISO 9001, an international standard on quality management systems, strengthening our quality assurance system consistently applied throughout all stages from development to production.
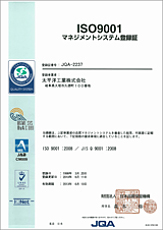
State of Acquisition of Management System Certification
Country | Company | ISO9001 | IATF16949 |
---|---|---|---|
Japan | Pacific Industrial Co., Ltd. | Mar. 1998 | - |
Pacific Engineering Corporation | May 1997 | Sep. 2018 | |
South Korea | Pacific Valve Industrial Co., Ltd. | Jul. 1999 | Jan.2018 |
Pacific Air Controls Co., Ltd. | - | Feb. 2018 | |
Taiwan | Pacific Valve Industrial Co., Ltd. | Aug. 2000 | - |
U.S.A. | Pacific Manufacturing Ohio, Inc. | Jan. 2013 | - |
Pacific Manufacturing Tennessee, Inc. | - | - | |
Schrader Bridgeport International, Inc. | Aug. 1998 | Dec. 2017 | |
Thailand | Pacific Industries (Thailand) Co.,Ltd. (Wellgrow Plant) | Nov. 2001 | Jan. 2018 |
Pacific Industries (Thailand) Co.,Ltd. (Rayong Plant) | - | - | |
China | Tianjin Pacific Auto Parts Co., Ltd. | - | Jul. 2018 |
Changsha Pacific Hanya Auto Parts Co., Ltd. | - | May 2018 | |
Pacific Auto Parts Technology(Changshu)Co.,Ltd. | Jul. 2016 | Nov. 2019 | |
France | Schrader SAS | 1996 | Jun. 2017 |
Aiming to Become a No.1 Manufacturer by “Manufacturing with Persistency”
The Pacific Industrial Group recognizes that human resource development is the very foundation of manufacturing. We are committed to passing on our manufacturing DNA and reducing costs for further evolution. Our manufacturing practices are based on the Toyota Production System, and we take the Genchi Genbutsu approach to implement KAIZEN (improvement) initiatives Groupwide.
Each of our bases is conducting proactive initiatives, such as improving quality through the voluntary introduction of an award system, or facilitating the passing on of technical skills to the younger generation.
Since FY2021, our Toyota Production System Voluntary Study Group has been working on KAIZEN initiatives for plastic molding products, mainly wheel caps, which are one of our main products. We are continuing this activity under the theme of "Aiming to be No.1 in competitiveness" to contribute to our business. We vigorously pursue increased production volume through labor savings, and reductions in paints and molding material usage in consideration of reducing environmental impact. We are promoting this as an activity that will not only change the future of manufacturing, but also lead to the development of human resources.
Overseas, too, our products have been highly evaluated in various countries in terms of quality, cost, delivery time, and other factors by Japanese manufacturers and overseas manufacturers alike. As a result of this global commitment to manufacturing, we received 14 global awards from our customers in FY2022.
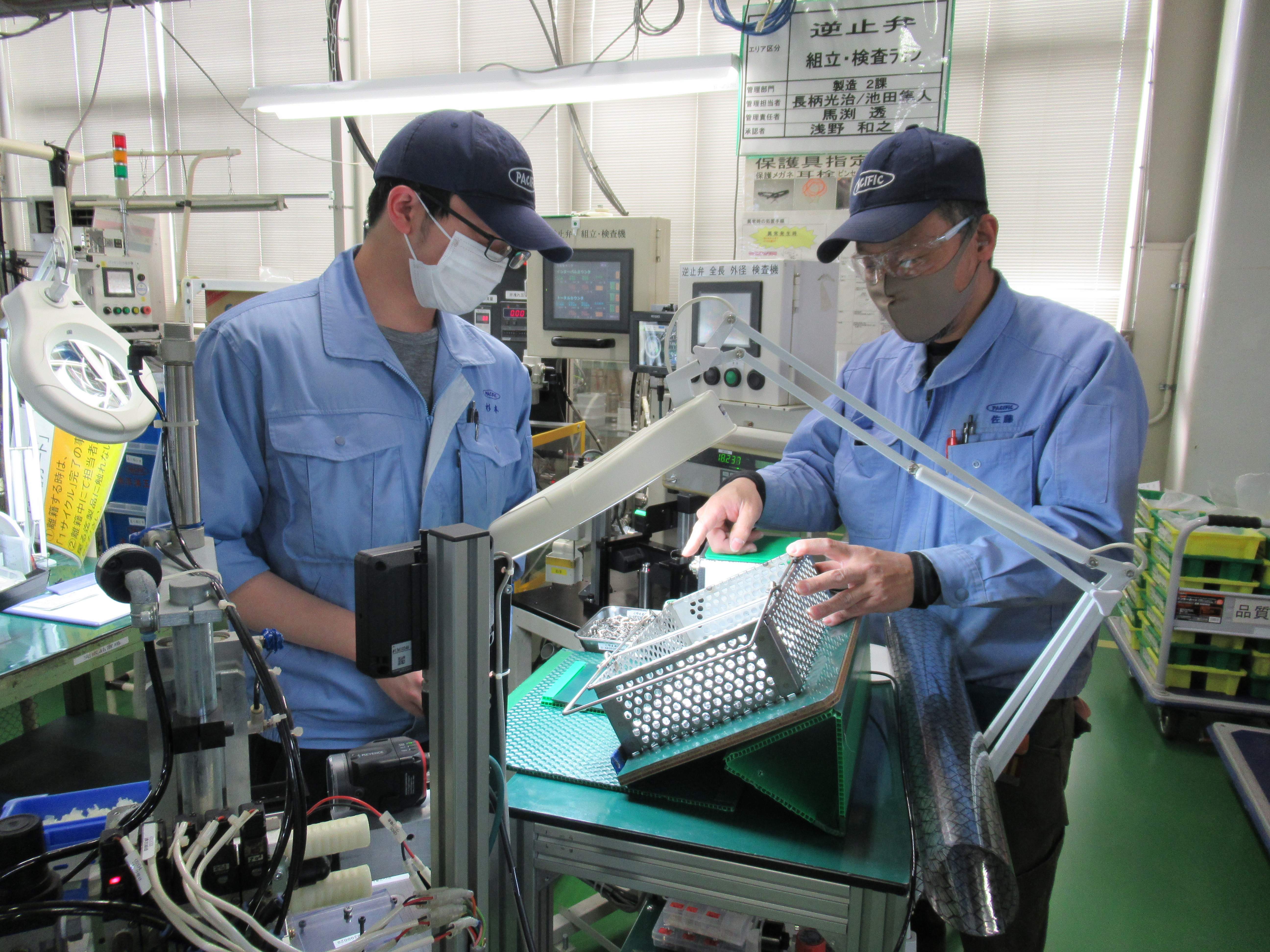
Enhancing Customer Satisfaction
We make continuous improvements based on the information collected from customers by our Sales and Quality Departments, and enhance customer satisfaction so that we can meet customers’ needs and expectations. We also hold technology exhibitions and give technical presentations in and outside Japan to introduce our new products, technologies, and methods to customers. SDGs and CO2 reduction are issues of great interest to our customers, and so we also focus on proposing products that contribute to achieving them.
At the request of our customers, we are participating in the CDP supplier program, and have been evaluated by EcoVadis, a global CSR evaluation organization for suppliers, who awarded us with their 2023 Bronze Medal.
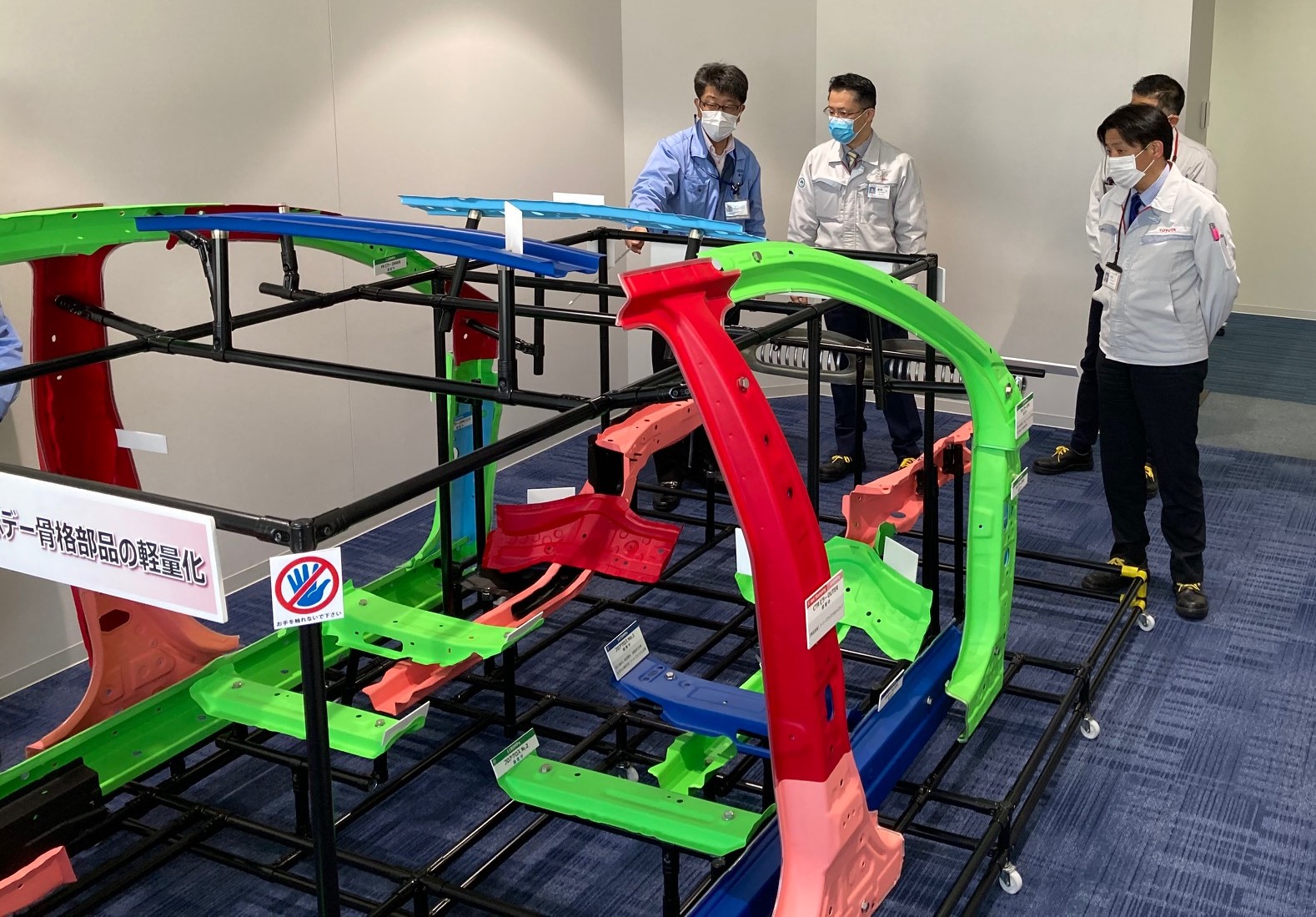