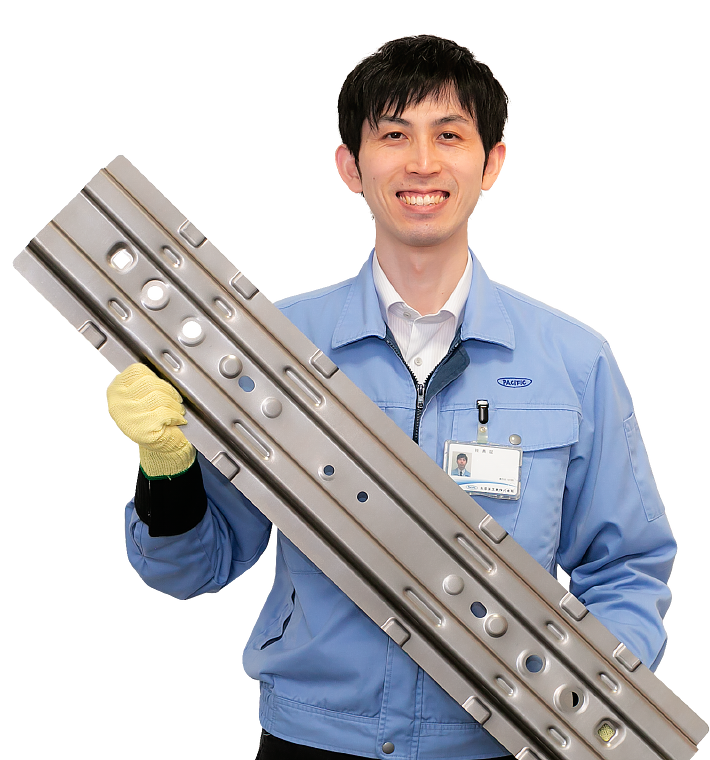
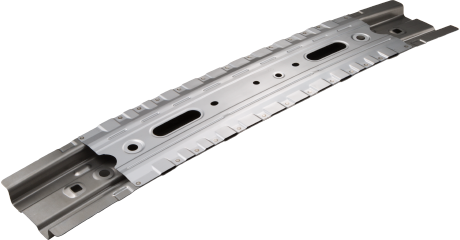
超ハイテン冷間プレス工法による、車両軽量化と環境配慮への取り組み
M.K
品質確保に欠かせない、プレス成形の解析技術
車体の骨格にあたる部分は、主にプレス成形により製造しています。プレス機械に取り付けた金型で板状の鋼材やアルミニウム合金材に段階的に圧力を加えることで、製品形状に成形していきます。そこで欠かせないのが、CAE解析※です。製品データをもとに実際の成形工程形状でモデルを作り、それをコンピュータ上で解析を行って不具合等がないかを確認します。プレス成形中に製品となる材料が割れたり、しわが発生したりしないかを検証し、不具合があれば形状変更や仕様の再検討などの改善を行い、見極めを行った上で、金型設計・製作、生産準備へと移行し、量産へとつなげていきます。
※CAE解析…Computer Aided Engineeringの略称で、コンピュータを用いたシミュレーションや解析のこと
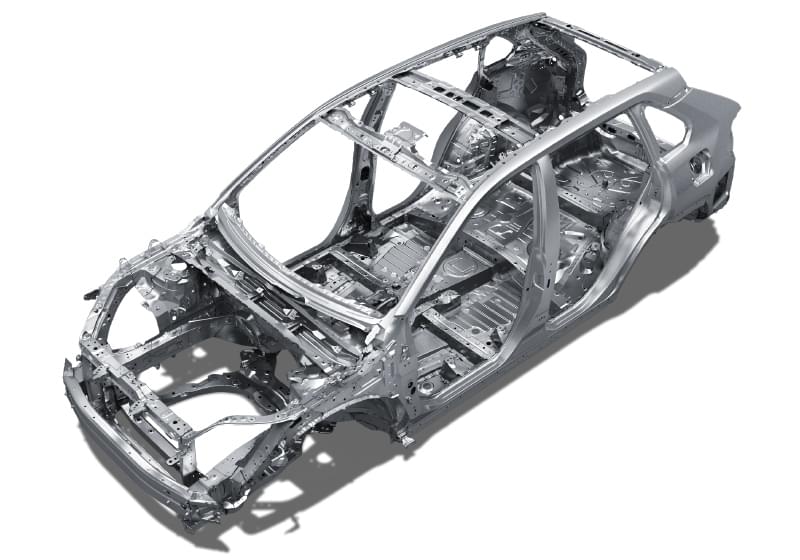
市場ニーズに応える、超ハイテン材への挑戦
車両の軽量化と衝突安全性、燃費の向上は、自動車製造において常に課題となります。さらに近年は、LCA(ライフサイクルアセスメント)やカーボンニュートラルの観点から、環境にも配慮した自動車が求められています。そこで材料として注目されるのが、超ハイテン材と呼ばれる超高張力鋼板です。より引張強さが高い材料でプレス成形を行うことで材料を薄くすることができ、強さと軽量化の両立が可能となります。当社では、従来の引張強さ1180MPa材から、さらに高強度な1470MPa材での製品化を、冷間プレス工法の開発により実現しました。
超ハイテン材の伸びにくくひずみにくいという特性上、加工後に材料を金型から取り出すと元の形状に戻ってしまうスプリングバック現象が発生します。1470MPa材は従来よりもスプリングバック量が非常に大きいため、CAE解析を使って目に見えない応力(元に戻ろうとする力)を分析してうまくスプリングバックを制御し、金型を作り込んでいきました。そうすることで、素材の持つ強度バラつきに対しても安定した精度でプレス成形できる製品の開発に成功しました。
また1180MPa以上の超ハイテンでは、プレス成形後の引張残留応力に起因する遅れ破壊の懸念があり、その対策も踏まえた応力制御を行っています。
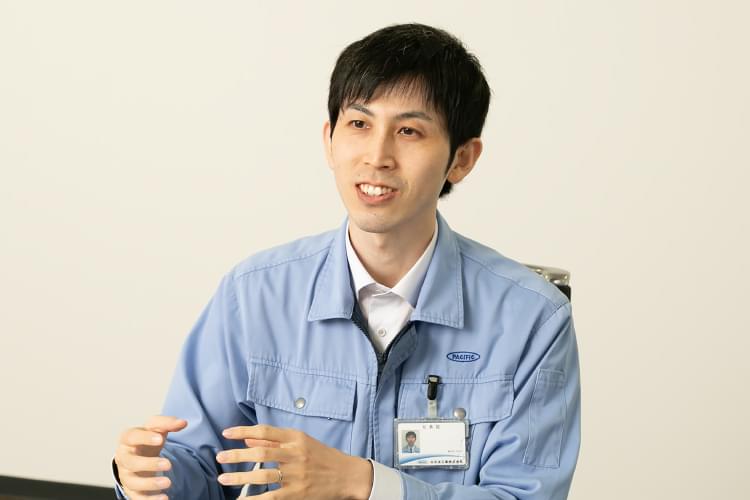
CO2削減に貢献する冷間プレス工法
当社ではこの1470MPa材を、冷間プレス工法により成形するノウハウの蓄積を進めています。冷間プレス工法は、材料に熱を加えることなく常温でプレス成形を行います。材料である鋼板を約900℃に加熱して成形するホットスタンプ工法と比較すると、生産時のCO2排出量が約1/8倍(当社試算)となります。さらに、ホットスタンプ工法は加工中に冷却時間を要しますが、冷間プレス工法はその時間がないため、生産スピードが格段に向上するのもメリットです。こういった生産工程の中でのCO2排出量にも配慮し、当社ではホットスタンプ工法から冷間プレス工法に置き換える取り組みを積極的に推進していきたいと考えています。
これらの成果として、レクサスNXに1470MPa材冷間プレスのルーフセンターリインフォースメントが採用されました。これは従来比22%の軽量化を実現しています。当社では3000tクラスの大型のプレス機を国内外の各拠点に持っており、現地で生産することが可能です。この環境を活かし、1470MPa材冷間プレスの部品を他車にも適用拡大していければと考えています。
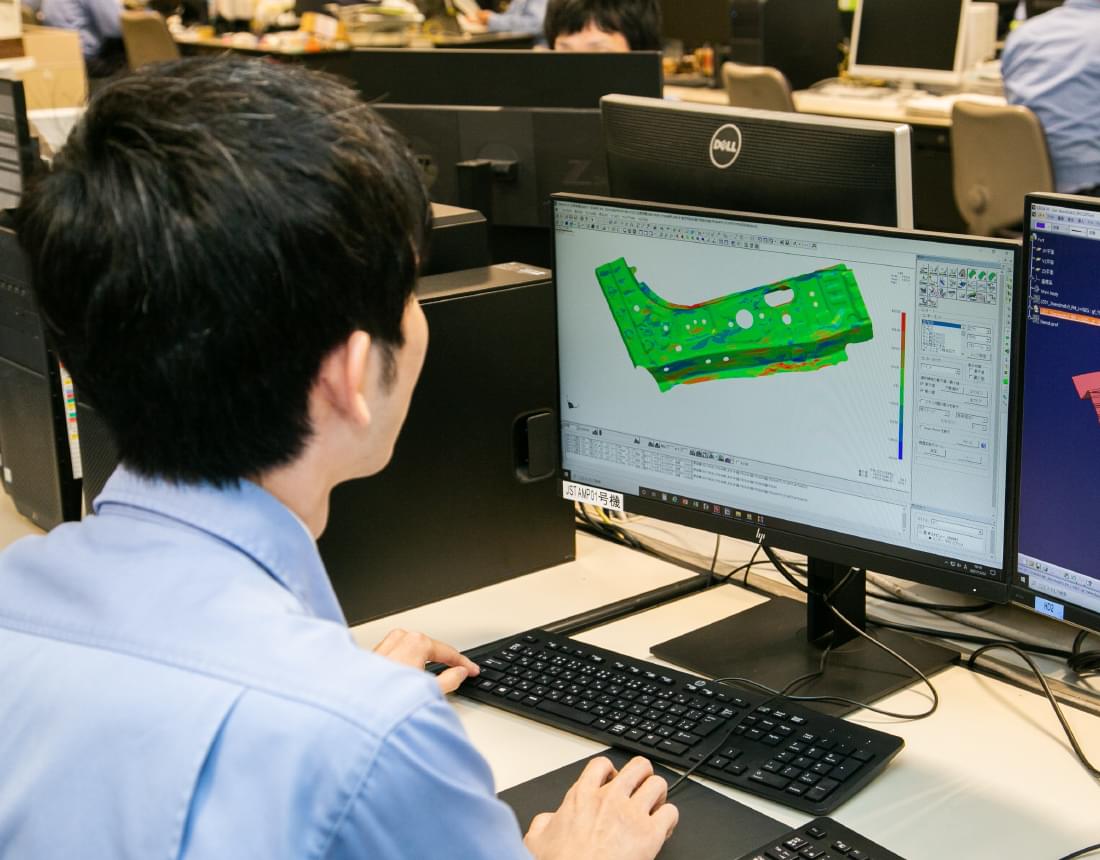
技術者としてのこだわり、思い
CAE解析の技術者として、誰もがWin-Winになるような仕事をしたいと思っています。不具合がない解析結果をめざすのはもちろん、後工程の金型製造でも解析通り不具合がなく、要求精度がクリアできる。量産現場でもスムーズな工程・工法で量産ができる。そしてお客様のもとに届いた後も安心安全に使っていただける、残留応力までコントロールされた製品を提供していきたいです。
まずは、超ハイテン材の使用が当たり前になりつつある市場背景の中で、お客様に当社の製品を採用してもらうために、技術力をさらにシンカ(深化、新化)する必要があります。従来培ってきたノウハウを活かしつつ、より高強度な材料に適用できる新工法を開発するなど、未来を見据えた開発に引き続き積極的に取り組んでいきたいと思います。