Technologies
Noise and vibration insulation
Multi-material Sheet Stamping Technology
This technology realizes a three-layer structure of GFRP(Glass Fiber Reinforced Plastics), GMT(Glass-Mat reinforced Thermoplastics), and steel.
This engine undercover is made of GFRP, which is as strong as steel but lighter, and is 76% lighter than conventional covers. In addition, the replacement of steel with resin improves the anti-corrosion performance.
High appearance urethane foam molding
We have a molding method that enables manufacturing using only polyurethane foam thanks to the development of a special polyurethane foam material. We have realized a weight reduction of 24% for the engine covers that adopt this technology compared to conventional products as we use lightweight polyurethane foam. In addition, by integrating fastening parts and eliminating coating, costs have been reduced by 27% compared to conventional products. Using flexible polyurethane foam also contributes to improved pedestrian protection.
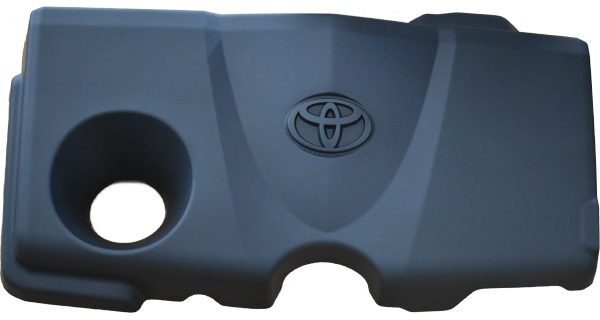

Integrated molding of nylon and urethane
Polyurethane foam, which is a vibration-proof material with a high sound-absorbing effect, is integrally foamed on the back surface of the nylon engine cover, and exhibits excellent sound-absorbing, sound-insulating, vibration-proofing, and vibration-damping performance. In addition, polyurethane foam can also withstand the harsh environment of an engine compartment with its heat resistance, and due to foam molding technology that makes use of shape flexibility and low-noise designs that are gentle on the surroundings, engine noise is greatly reduced.
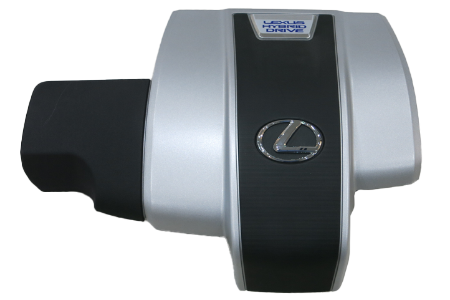
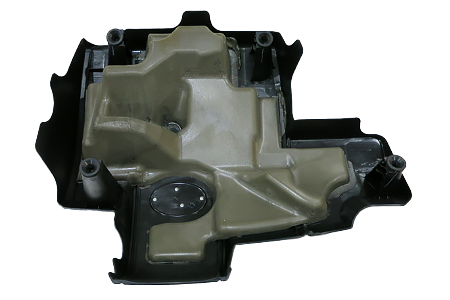
Base form molding
The nylon resin cover is foamed internally to reduce the amount of resin used, thereby reducing weight and cost. In addition, it also has a paint-free exterior and realizes the same rigidity as conventional methods (solid). We have achieved a weight reduction of 30% for the engine covers that adopt this technology compared to conventional products.
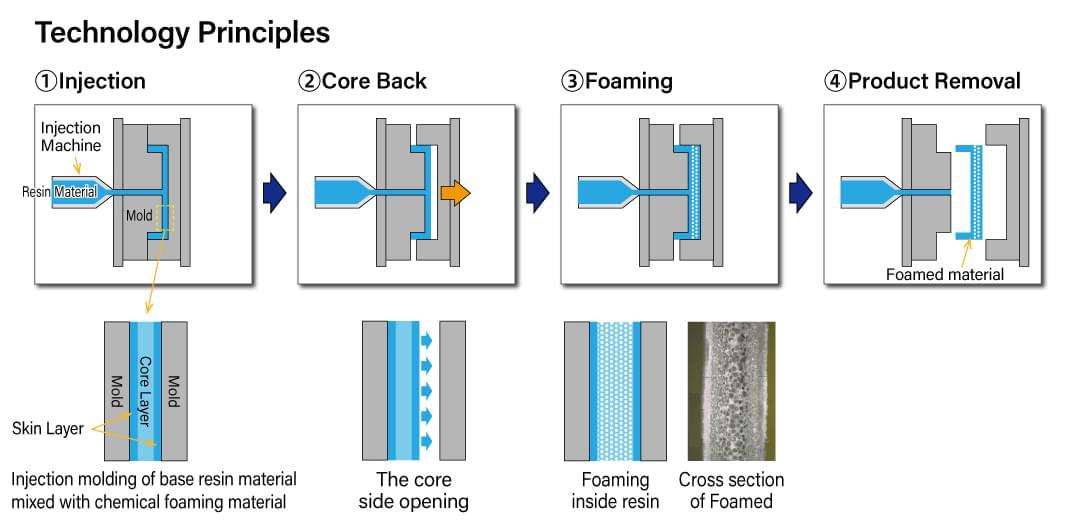
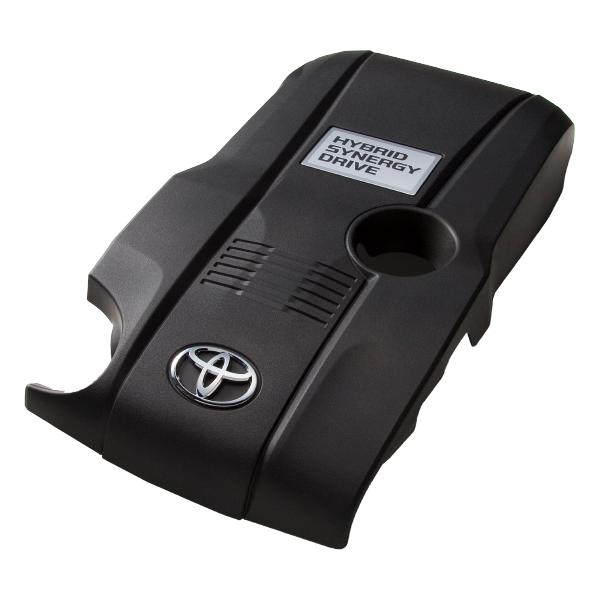
Decorating
In-mold Transfer
This method is integrated process of injection molding and transfer painting.
The transfer machine sends a transfer foil into mold die and positioned.
When processing injection molding, transfer painting is processed by heat pressure.
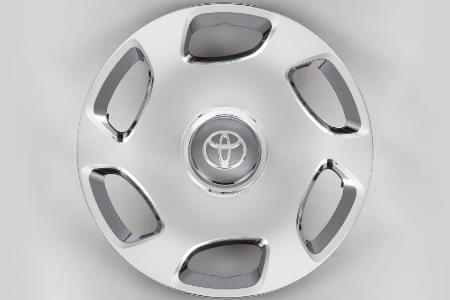
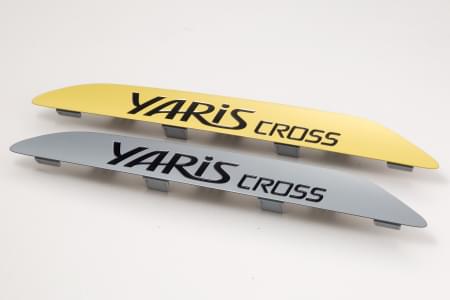
Luster Film Molding Technology
Special film is preformed 3dimensional shape and installed in die mold.
The special film is formed with resin (injection molding) by welding to form the finished parts.
Deep drawability of film improves design.
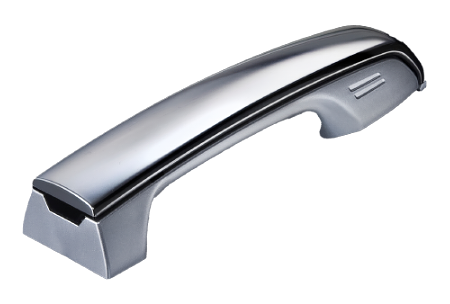
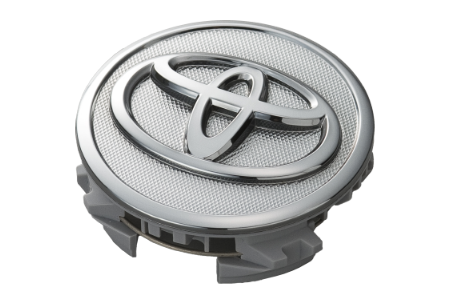
Painting
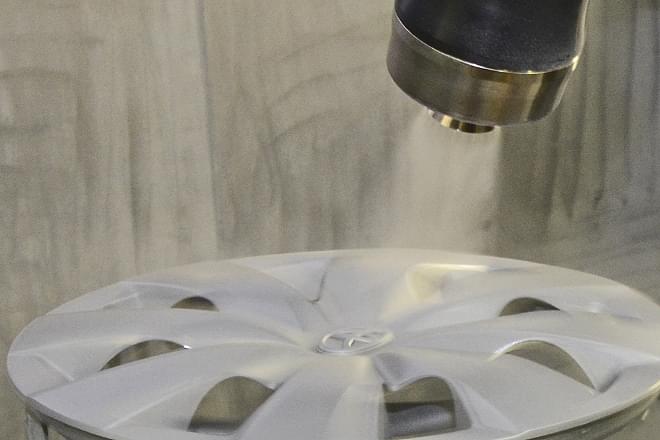
We use surface processing that gives color by coating the surface of the material and drying it. With this coating, it is possible to color products in various colors. In addition to conventional metallic coating, we also excel at metallic coating with a lustrous feel and mask coating in which a single part is coated with various colors.
Plating
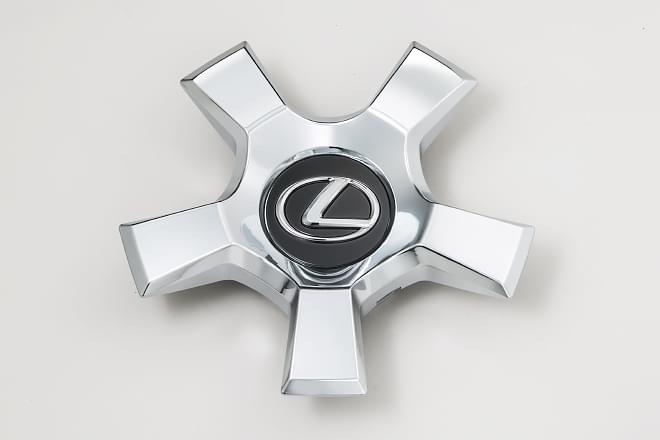
This is a surface treatment that makes a resin molded product covered with a metallic film. It is possible to apply a luxurious metallic color tone to the surface, and it is also possible to create a metallic feel with different color tones and luster.
Hot Stamp Decorating (Thermal Transfer Film)
Thermal transfer technology is a processing technology that transfers metallic characters, designs, etc. by pressurizing and heating hot stamping foil.
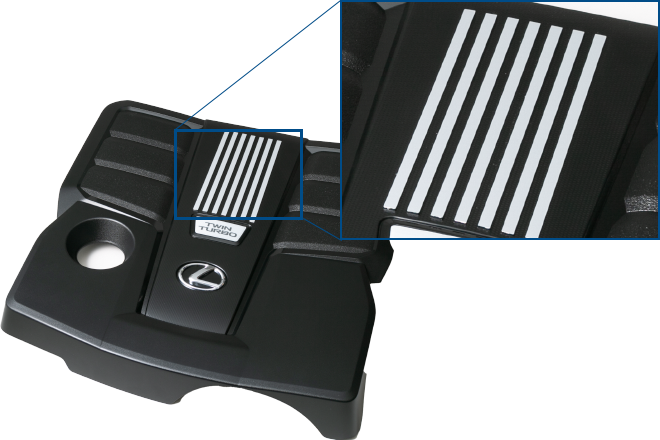
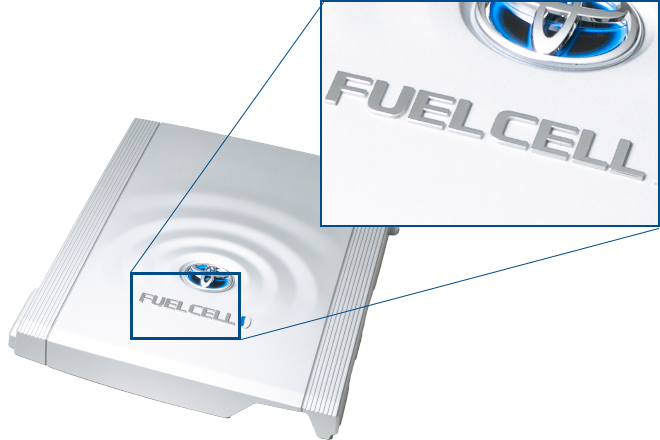
Integrated production
Integrated production line for wheel caps
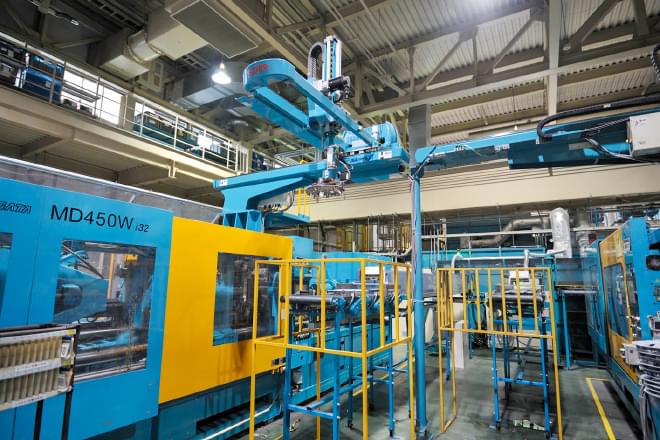
By converting wheel caps to an integrated production line, we have constructed a line that has shortened the lead time from molding to coating and assembly.
We constructed the line in pursuit of labor-saving and space-saving, under the concept of a line that responds strongly to production fluctuations and that will be easy to roll out globally. It is an innovative line that pursues cost reductions.
Analysis
Acoustic analysis
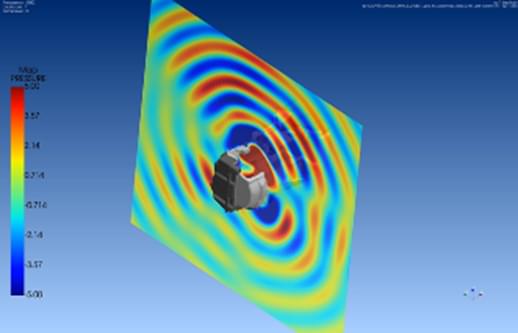
By analyzing the basic characteristics of sound, it is possible to visualize sound and propose optimal shapes.
Flow analysis
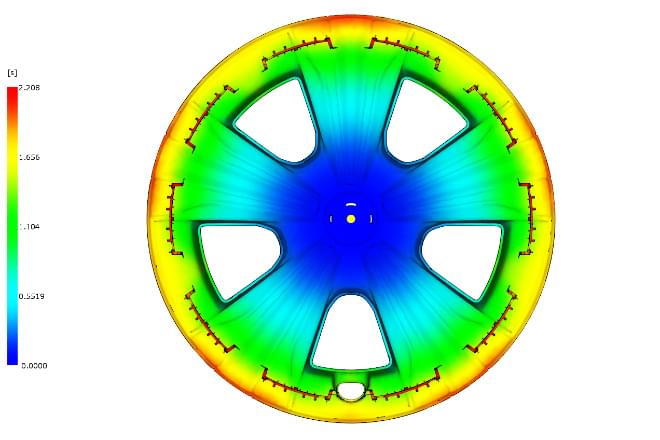
We reduce product defects and the number of trial processes by predicting the pressure, temperature and curvature deformation of resin during injection molding, and determining the product shape and mold specifications.
Structural analysis
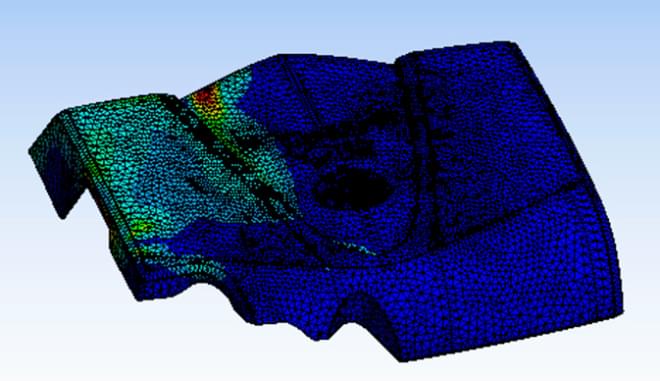
We can identify stress concentration points by analyzing the deformation and stress of products due to external and internal forces. Those results are incorporated into designs to prevent defects in advance.
Acoustic evaluation
NV evaluation device
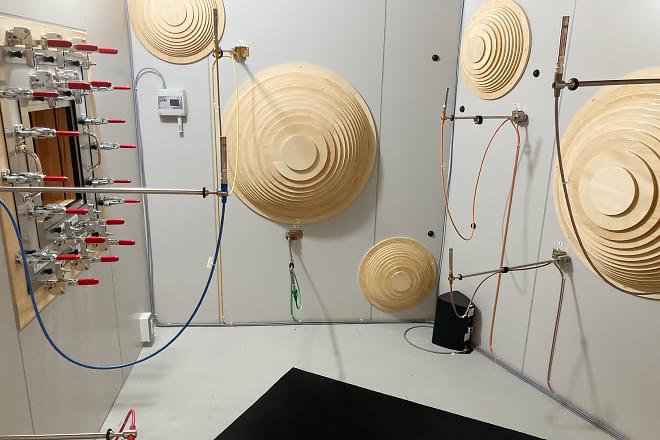
The company possesses large equipment capable of measuring sound absorption rates and transmission loss, and has established an environment enabling accurate measurement.
In addition, we also possess equipment that can evaluate the acoustics of the product itself and equipment that can visualize sound sources, making it possible to perform acoustic measurements even at the product level.
* NV: Noise / Vibration